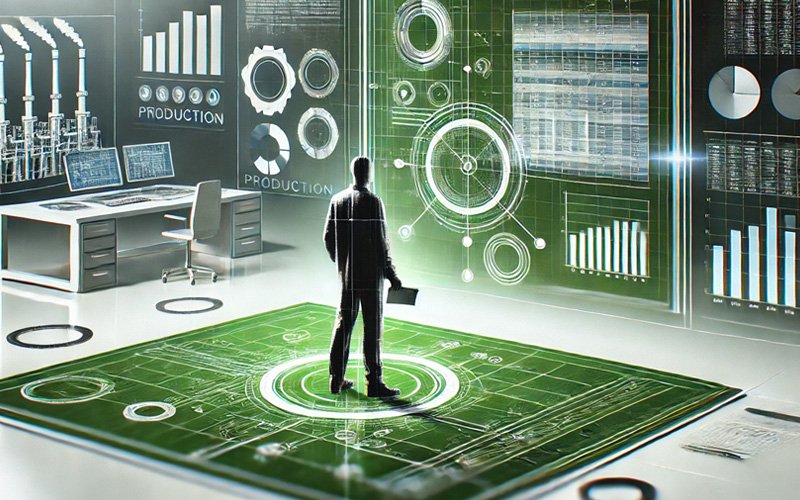
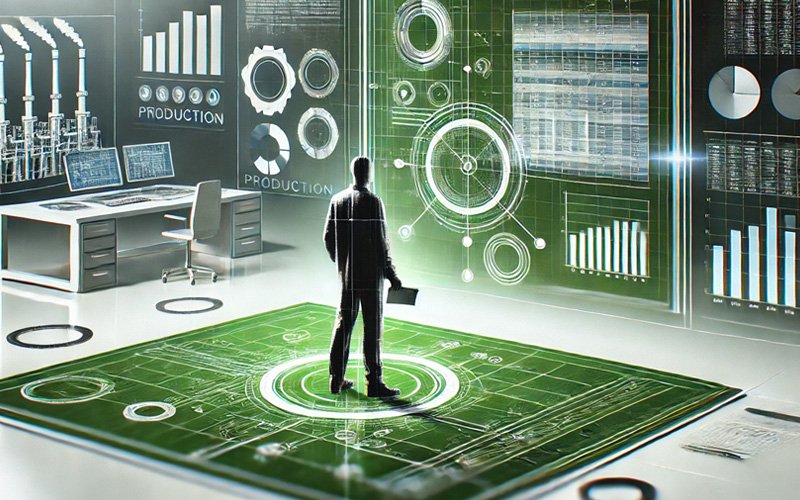
PPCP ou PCP: qual a diferença?
PPCP e PCP: Entenda as diferenças e escolha a abordagem certa para otimizar sua produção. A gestão da produção é um dos pilares mais importantes para o sucesso de qualquer empresa industrial. Dentro desse contexto, os termos PPCP e PCP aparecem frequentemente, mas será que todos sabem a diferença entre eles? Compreender essas diferenças pode ser a chave para otimizar processos e alcançar uma maior eficiência produtiva. A proposta aqui não é estabelecer um termo correto, mas sim explorar o histórico e as razões por trás da inclusão de um novo “P” no tradicional PCP. Entender essa diferença é fundamental para refletir e discutir sobre a evolução das práticas de planejamento e controle da produção. Histórico e evolução O PCP (Planejamento e Controle da Produção) surgiu como uma ferramenta essencial para gerenciar as atividades produtivas de forma eficiente. Ele envolve o planejamento das necessidades de produção, a programação das atividades e o controle dos processos para garantir que os objetivos sejam atingidos. Em resumo, o PCP busca garantir que a produção ocorra dentro dos prazos, custos e qualidade esperados. Com o passar dos anos e a evolução das tecnologias e das exigências do mercado, surgiu a necessidade de um planejamento mais detalhado e adaptável. Foi nesse contexto que o PPCP (Planejamento, Programação e Controle da Produção) se consolidou, adicionando a programação como um elemento essencial. Essa mudança não se trata apenas de uma nova terminologia, mas sim de uma evolução significativa na maneira como as atividades produtivas são gerenciadas. A importância da programação A adição de programação no modelo tradicional de PCP veio para atender à necessidade de um planejamento mais detalhado e preciso das atividades de produção. Enquanto o PCP trabalha com uma visão mais macro, o PPCP permite um olhar mais minucioso e dinâmico sobre cada etapa do processo produtivo, integrando tecnologias avançadas e softwares especializados que ajudam a prever e resolver problemas antes que eles aconteçam, otimizando o uso dos recursos e minimizando desperdícios. A programação envolve a definição de sequências de operações, horários específicos para cada atividade e a alocação precisa dos recursos. Isso possibilita uma maior flexibilidade e capacidade de resposta às mudanças do mercado, garantindo que a produção se mantenha eficiente e competitiva. Ferramentas para planejamento e programação: Opcenter APS Para atender a essas novas exigências, diversas ferramentas e softwares foram desenvolvidos. No contexto do planejamento e programação (PP), o software Opcenter APS da Siemens se destaca. Este software é projetado para fornecer um planejamento e programação avançados, permitindo que as indústrias criem sequenciamentos detalhados, simulem cenários e otimizem suas operações. O Opcenter APS oferece diversas funcionalidades que ajudam a melhorar a eficiência da produção, como: Planejamento detalhado: permite criar planos que consideram todas as restrições e capacidades da fábrica (capacidade finita). Simulação de cenários: facilita a previsão de problemas e a busca por soluções antes que eles ocorram. Otimização das operações: ajuda a encontrar o melhor uso dos recursos, reduzindo tempos de produção e custos. Controle da produção com Opcenter X Para o controle da produção (CP), o Opcenter X é a ferramenta ideal. Este software MES (Manufacturing Execution System) da Siemens oferece um monitoramento robusto e em tempo real de todas as operações. Ele permite acompanhar o progresso da produção, identificar e resolver problemas rapidamente, além de integrar-se com outros sistemas para proporcionar uma visão completa e integrada da produção. O Opcenter X oferece: Monitoramento em tempo real: acompanhamento contínuo das operações para detectar e resolver problemas imediatamente. Análise de desempenho: avaliação constante da eficiência das operações, identificando áreas para melhorias. Integração com outros sistemas: conexão com outras ferramentas de gestão para uma visão completa e integrada da produção. A APS3 como parceira da Siemens A APS3 é uma parceira estratégica da Siemens, especializada no diagnóstico e implementação dos sistemas Opcenter APS e Opcenter X. Com uma equipe experiente e altamente qualificada, a APS3 oferece soluções personalizadas que atendem às necessidades específicas de cada cliente, garantindo que eles possam tirar o máximo proveito dessas ferramentas avançadas. Os benefícios de trabalhar com a APS3 incluem: Diagnóstico detalhado: identificação precisa das necessidades e desafios da sua produção. Implementação eficiente: instalação e configuração dos sistemas de maneira rápida e sem interrupções. Suporte contínuo: assistência técnica e treinamentos para garantir que sua equipe esteja sempre atualizada e aproveitando ao máximo as ferramentas. Para mais informações sobre como a APS3 pode ajudar sua indústria a implementar o PPCP e melhorar a eficiência da sua produção, clique aqui e descubra as soluções que temos para você.