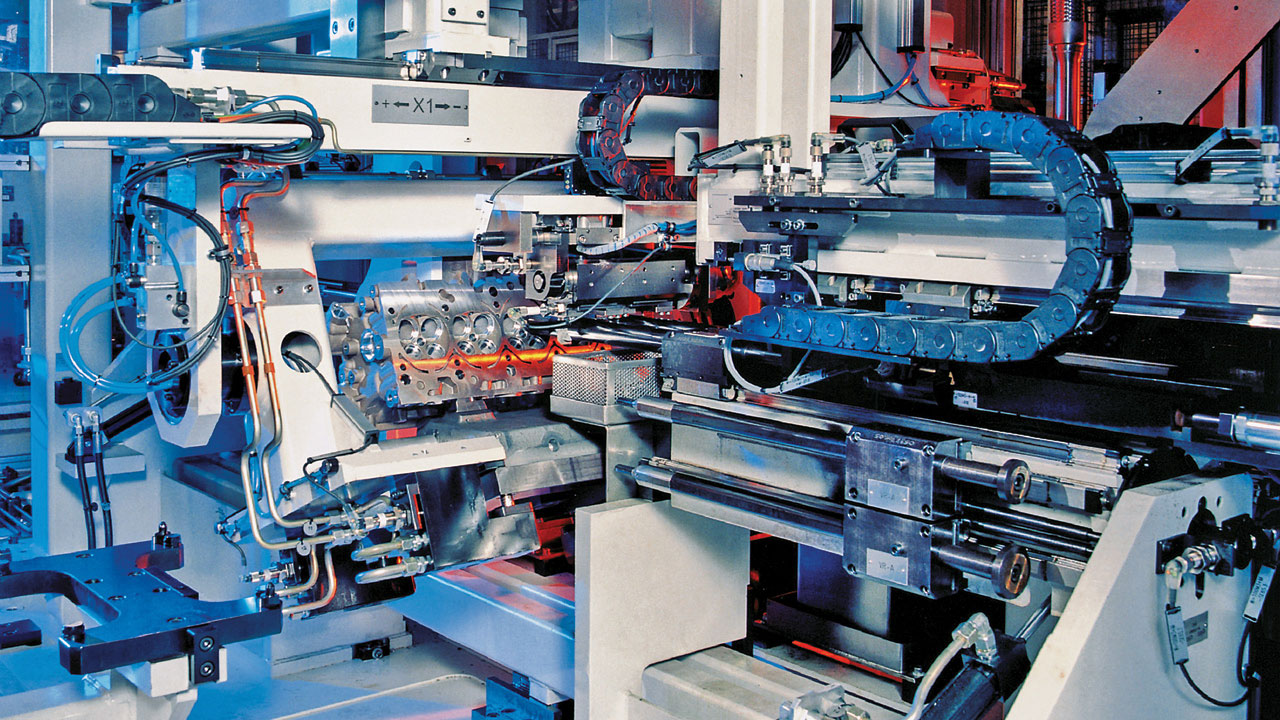
No ambiente industrial, cada minuto conta. Máquinas operando em perfeita sintonia garantem que a produção siga seu fluxo sem interrupções.
Mas quando um equipamento essencial quebra de maneira inesperada, o efeito dominó pode ser catastrófico: prazos comprometidos, desperdícios de materiais, retrabalho, custos adicionais e perda de eficiência.
O maior problema é que muitas indústrias não possuem total visibilidade sobre os impactos dessa falha até que ela já tenha gerado prejuízos irreversíveis. A capacidade de antecipar e minimizar os danos é o que diferencia uma operação bem estruturada de outra que constantemente precisa “apagar incêndios”. Vamos explorar as consequências de uma quebra de máquina e entender como a tecnologia pode reduzir esses riscos.
O desafio: os impactos ocultos de uma falha inesperada
Quando um equipamento essencial para a produção apresenta problemas, o primeiro reflexo é a busca por soluções emergenciais. A equipe de manutenção é acionada, mas muitas vezes não há peças de reposição disponíveis de imediato. Enquanto isso, o estoque de matéria-prima continua sendo consumido sem que o produto final possa ser entregue no prazo. O trabalho se acumula, os custos disparam e as decisões precisam ser tomadas sob pressão.
Se o problema ocorre em um setor crítico da fábrica, todo o sequenciamento da produção pode ser comprometido. Um equipamento responsável por uma etapa específica, como a usinagem de componentes ou a moldagem de peças plásticas, ao falhar, gera um efeito cascata. As operações subsequentes ficam paradas, trabalhadores ficam ociosos e os pedidos deixam de ser atendidos, impactando diretamente os clientes.
Além disso, a falta de um plano estruturado para lidar com esse tipo de imprevisto pode fazer com que as respostas sejam tomadas de forma desorganizada. Realocação de operadores, mudanças de última hora no planejamento e até compras emergenciais de peças acabam sendo necessárias, muitas vezes a um custo muito maior do que o previsto.
Agora, vamos analisar os principais impactos dessa falha no ambiente industrial.
Impacto 1: atrasos nas entregas e insatisfação dos clientes
Uma das consequências imediatas de uma falha inesperada é o atraso nos prazos de entrega. Quando um equipamento crítico para a produção deixa de operar, o cumprimento das datas prometidas aos clientes fica comprometido. Isso pode significar penalidades contratuais, perda de credibilidade e até mesmo o risco de o cliente buscar um concorrente que possa atender às suas demandas com mais previsibilidade.
Em segmentos que operam sob contratos rígidos, como o automotivo, onde peças e componentes precisam ser entregues em datas exatas para evitar a interrupção da montagem dos veículos, qualquer atraso pode gerar um efeito dominó. A falha de um fornecedor pode atrasar a produção de uma linha inteira, comprometendo não apenas a empresa afetada, mas toda a cadeia produtiva.
Para evitar esse cenário, algumas empresas recorrem a soluções emergenciais, como produção em turnos extras e fretes expressos, o que eleva significativamente os custos operacionais. O problema é que essas ações de correção muitas vezes não são sustentáveis a longo prazo e podem comprometer a rentabilidade do negócio.
Impacto 2: aumento do trabalho em processo (WIP) e desorganização do fluxo produtivo
Quando uma máquina essencial para a produção para inesperadamente, os materiais que estavam em processamento ficam retidos no sistema, gerando um acúmulo de trabalho em andamento (WIP – Work In Progress). Esse acúmulo não apenas reduz a eficiência da produção, mas também causa desorganização nos setores de armazenagem e logística interna.
Se a paralisação ocorre em uma etapa inicial da produção, as demais fases ficam sem insumos para operar, criando gargalos que podem levar dias para serem resolvidos. Por outro lado, se a falha ocorre em uma etapa final, os setores anteriores continuam produzindo sem conseguir escoar a produção, resultando em excesso de materiais estocados e desperdício de espaço.
Além disso, a necessidade de redistribuir tarefas e operadores para outras atividades gera desbalanceamento na fábrica. Se uma linha de montagem precisa ser temporariamente suspensa, operadores podem ser deslocados para funções que não dominam completamente, impactando a produtividade e aumentando o risco de erros e retrabalho.
Impacto 3: custos elevados de manutenção e desperdício de recursos
A manutenção corretiva de uma máquina quebrada custa muito mais do que um reparo programado. Quando uma peça falha inesperadamente, a empresa precisa agir rapidamente para encontrar um fornecedor que tenha o item em estoque e possa entregá-lo no menor prazo possível. Muitas vezes, isso significa pagar valores muito acima do normal ou recorrer a transportes urgentes para minimizar os impactos na produção.
Além dos custos diretos com manutenção emergencial, há ainda o desperdício de materiais. Em muitas indústrias, um processo interrompido no meio do ciclo produtivo pode tornar o lote inteiro inviável, exigindo o descarte de insumos já utilizados. Isso afeta diretamente a margem de lucro e pode resultar em prejuízos financeiros expressivos.
Outro fator relevante é o impacto na confiabilidade dos equipamentos. Quando uma máquina falha repetidamente sem um plano adequado de monitoramento e manutenção preditiva, o problema se torna recorrente. Isso significa mais custos ao longo do tempo, além do risco de perda de eficiência e aumento da taxa de defeitos nos produtos.
Impacto 4: gargalos inesperados e desbalanceamento da fábrica
Cada setor da fábrica depende de um fluxo produtivo alinhado para funcionar corretamente. A quebra de um equipamento pode alterar completamente o balanceamento da operação, criando gargalos que antes não existiam. Isso obriga o PPCP (Planejamento, Programação e Controle da Produção) a revisar toda a estratégia, realocar máquinas e operadores e buscar alternativas emergenciais.
O problema é que, sem ferramentas adequadas para simular cenários e reorganizar a produção de forma eficiente, as decisões acabam sendo tomadas com base na intuição, e não em dados concretos. Isso pode gerar uma distribuição ineficiente dos recursos produtivos, aumentando ainda mais os atrasos e os custos.
Como evitar os impactos de uma quebra inesperada?
A solução para minimizar os danos de uma quebra de máquina não está apenas na manutenção preventiva, mas também na capacidade de simular cenários e reprogramar a produção rapidamente. O Opcenter APS, da Siemens, é uma ferramenta de planejamento e programação avançada da produção que permite que empresas prevejam possíveis falhas e reajam de forma rápida e estratégica.
Com essa solução, é possível:
✔️ Simular falhas e avaliar seus impactos, permitindo uma tomada de decisão mais informada.
✔️ Testar diferentes cenários de resposta, garantindo que a melhor estratégia seja adotada antes mesmo de um problema ocorrer.
✔️ Reprogramar a produção automaticamente, redistribuindo ordens de forma otimizada e minimizando paradas.
✔️ Reduzir o tempo de resposta a imprevistos, garantindo maior estabilidade no fluxo produtivo.
Com o Opcenter APS, as empresas deixam de ser reativas e passam a ter um controle estratégico sobre o que acontece no chão de fábrica, garantindo maior previsibilidade e eficiência.
APS3: sua parceira na digitalização da indústria
Na APS3, entendemos os desafios enfrentados pelo setor produtivo e oferecemos soluções que transformam problemas em oportunidades. Como agentes Siemens, auxiliamos empresas a implementar o Opcenter APS, permitindo um planejamento mais inteligente, uma programação eficiente e uma gestão proativa das operações.
Quer evitar que falhas inesperadas impactem sua produção? Clique aqui e conheça nossas soluções.