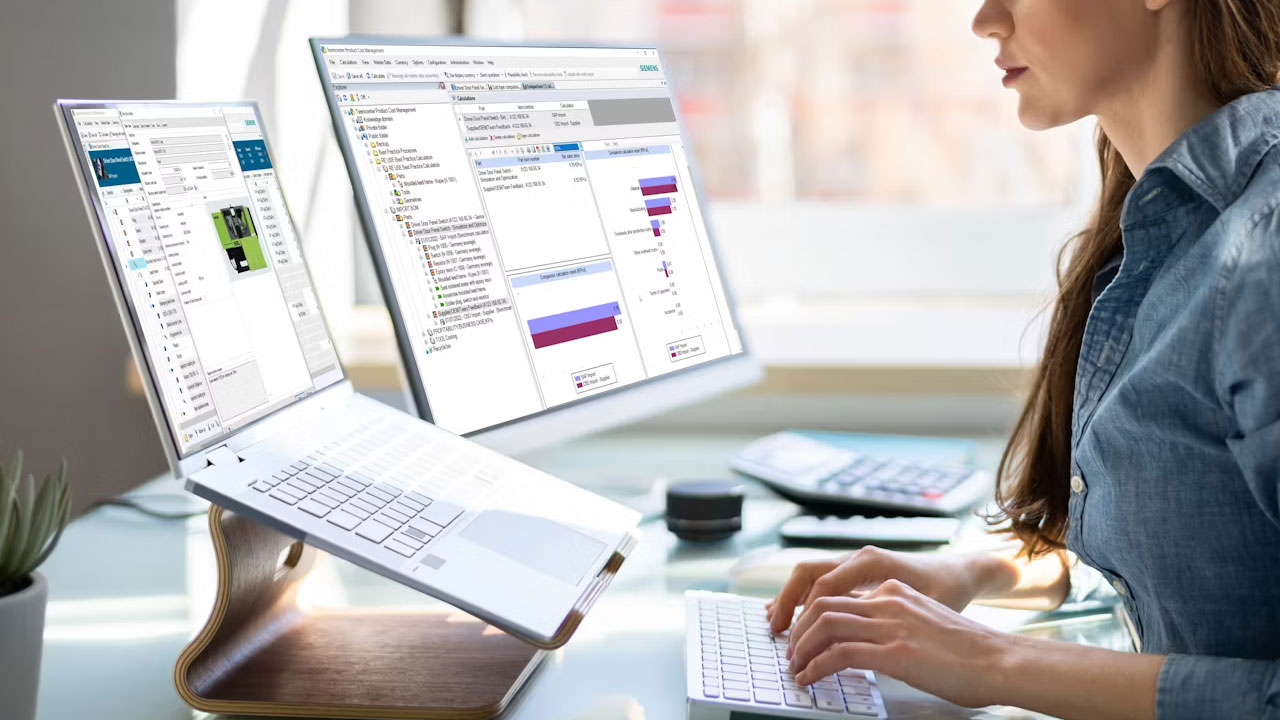
A engenharia e a produção industrial precisam operar como um sistema bem sincronizado. Qualquer falha nesse elo pode gerar impactos diretos nos custos operacionais da fábrica.
Projetos mal documentados, falta de padronização e erros de comunicação entre os setores resultam em desperdícios, retrabalho e atrasos que comprometem a competitividade da empresa. Quando a engenharia não trabalha com dados precisos e bem estruturados, a manufatura paga a conta com correções de última hora, baixa produtividade e desperdício de materiais.
Mas como garantir que a fábrica receba informações confiáveis, sem precisar lidar com mudanças inesperadas no meio da produção? A resposta está na integração eficiente entre engenharia e manufatura.
O impacto de erros na engenharia sobre os custos produtivos
Na prática, falhas na engenharia resultam em prejuízos financeiros para a empresa. Erros em projetos, falta de padronização e comunicação falha entre engenharia e produção geram retrabalho, desperdício de materiais e atrasos, afetando a produtividade e a competitividade da indústria.
Erros de projeto e desperdício de materiais
Imagine uma fábrica de peças automotivas onde um erro dimensional em um projeto só é detectado no chão de fábrica. O resultado? Peças rejeitadas, retrabalho na linha de produção e perda de matéria-prima. Esse tipo de problema ocorre porque, sem uma verificação criteriosa dos requisitos de fabricação, inconsistências passam despercebidas na fase de desenvolvimento e só são corrigidas quando já impactam a produção.
Mudanças de última hora e custos extras
Alterações no projeto quando a produção já começou geram desorganização e custos elevados. Para adaptar-se a um novo design, a fábrica pode precisar interromper máquinas, reprogramar operações, treinar operadores novamente e, em alguns casos, até descartar lotes inteiros de produtos obsoletos. Além do impacto financeiro, mudanças tardias afetam prazos e a confiabilidade da entrega.
Falta de controle sobre versões e especificações
Quando não há um fluxo padronizado para gestão de versões dos projetos, o setor produtivo pode acabar trabalhando com especificações desatualizadas. Se uma alteração não for devidamente comunicada, operadores continuam fabricando peças fora dos novos padrões, gerando reprocessamento e atrasos na entrega.
Roteiros de fabricação manuais e falhas no processo
A engenharia de processos, muitas vezes, ainda cria roteiros de fabricação manualmente, sem integração com produto e produção. Isso significa que o setor produtivo recebe um roteiro cheio de erros, que não reflete a realidade da fábrica. Mesmo quando melhorias são sugeridas, como a atualização do tempo padrão após uma cronoanálise, a revisão manual torna tudo lento e impreciso, dificultando a otimização contínua.
Instruções de trabalho desatualizadas e falta de rastreabilidade
Outro problema comum está nas instruções de trabalho, que detalham materiais usados, posicionamento, EPIs e diretrizes operacionais. Muitas fábricas ainda usam arquivos PDF desconectados do produto e da produção, exigindo atualizações manuais que geram inconsistências. Além disso, a falta de controle adequado desses documentos complica auditorias de certificação ISO, tornando o gerenciamento documental um gargalo operacional.
Os impactos dessas falhas vão muito além do chão de fábrica. Atrasos, desperdício de insumos e falta de padronização afetam custos, prazos e a competitividade da empresa. Por isso, investir na integração entre engenharia e manufatura é essencial para reduzir desperdícios e melhorar a eficiência operacional.
Retrabalho e desperdício: as armadilhas de uma engenharia mal integrada
Os custos gerados por falhas na engenharia vão além do impacto imediato no orçamento da fábrica. Retrabalho, desperdício de material e atrasos na produção prejudicam a eficiência geral da empresa e, em longo prazo, afetam a credibilidade da marca no mercado.
Quanto mais tarde um erro é identificado no desenvolvimento de um produto, maior será o custo para corrigi-lo. Quando a engenharia falha em padronizar processos ou comunicar mudanças de forma clara, a manufatura pode receber especificações desatualizadas, levando à produção de peças fora do padrão, acúmulo de refugo e necessidade de ajustes inesperados na linha de produção.
Mudanças tardias no projeto também exigem reprogramação da produção, realocação de materiais e, em alguns casos, até a interrupção temporária das operações, impactando diretamente os prazos e a produtividade.
Os principais problemas enfrentados pelas fábricas devido a uma engenharia mal integrada incluem:
- Retrabalho frequente: projetos incompletos ou mal especificados exigem ajustes constantes na produção, reduzindo a eficiência.
- Erros de fabricação: falta de controle sobre versões do projeto pode resultar na produção de peças fora das especificações.
- Desperdício de matéria-prima: problemas na documentação e na comunicação geram refugo desnecessário.
- Atrasos na entrega: falhas na integração entre engenharia e manufatura comprometem cronogramas e impactam a satisfação dos clientes.
Uma engenharia eficiente não significa apenas desenvolver produtos inovadores, mas garantir que eles possam ser produzidos com qualidade, no menor tempo possível e com o menor custo operacional.
Como melhorar a integração entre engenharia e manufatura
Para evitar esses problemas e garantir que a fábrica opere de forma eficiente, algumas estratégias podem ser implementadas:
- Padronização dos processos de engenharia
Documentar cada etapa do desenvolvimento do produto e garantir que todas as versões dos projetos estejam organizadas e acessíveis para a equipe de manufatura reduz a ocorrência de erros. - Automação da gestão de mudanças
Qualquer alteração em um projeto deve seguir um fluxo estruturado, permitindo que todas as áreas envolvidas sejam notificadas e possam se adaptar com antecedência. - Uso de um repositório centralizado de informações
Contar com um sistema que unifique todos os dados do produto, garantindo que a equipe de produção tenha acesso às versões mais recentes e corretas, evita confusões e retrabalho. - Melhoria na comunicação entre engenharia e produção
Criar canais eficientes de troca de informações, como reuniões periódicas, relatórios e ferramentas digitais, ajuda a alinhar expectativas e antecipar possíveis problemas. - Adoção de um software de PLM (Product Lifecycle Management)
Soluções como o Teamcenter PLM garantem um gerenciamento completo do ciclo de vida do produto, evitando problemas relacionados à falta de controle sobre versões, mudanças não documentadas e falhas na comunicação.
Como o Teamcenter PLM reduz custos e melhora a eficiência da manufatura
A integração entre engenharia e manufatura é fundamental para eliminar falhas no desenvolvimento e reduzir custos produtivos. O Teamcenter PLM, solução de gerenciamento do ciclo de vida do produto, possibilita que todas as informações fiquem centralizadas em um único ambiente digital, garantindo que a manufatura opere sempre com dados atualizados e confiáveis.
Empresas que adotam esse modelo conseguem minimizar retrabalho, desperdício de materiais e atrasos na produção ao evitar que erros de projeto cheguem ao chão de fábrica. A estratégia de Shift Left aplicada ao desenvolvimento de produtos reforça essa abordagem, pois antecipa falhas antes mesmo da fabricação, por meio da simulação e validação digital.
Além disso, a integração entre engenharia e manufatura via PLM permite um controle preciso das mudanças, reduzindo os riscos de inconsistências entre projeto e produção. Isso acontece porque o Teamcenter PLM estrutura a conexão entre EBOM e MBOM, além de levar o planejamento dos processos para dentro do desenvolvimento do produto, garantindo que os roteiros de fabricação reflitam as atualizações feitas no design do produto.
Outro ponto essencial é a digitalização e integração das instruções de trabalho, eliminando a necessidade de documentos estáticos e PDFs que exigem atualizações manuais. Qualquer alteração realizada na engenharia é automaticamente propagada para os operadores no chão de fábrica, garantindo conformidade com normas e certificações sem os desafios de rastreabilidade da documentação física.
A integração do PLM com sistemas avançados de planejamento e programação da produção também é um fator estratégico. A conexão entre Teamcenter e Opcenter APS possibilita um planejamento mais ágil e eficaz, garantindo que decisões de produção sejam baseadas em dados atualizados e alinhados com a demanda real.
Com essa abordagem, a empresa pode:
- Gerenciar mudanças com precisão: toda modificação no projeto segue um fluxo automatizado, garantindo que todos os setores recebam informações atualizadas.
- Reduzir desperdícios: maior controle sobre especificações evita falhas que resultam em refugo e retrabalho.
- Melhorar a colaboração entre equipes: integração eficiente entre engenharia e produção reduz falhas na comunicação.
- Garantir conformidade com normas e padrões: rastreabilidade digital de cada etapa do ciclo de vida do produto assegura cumprimento de requisitos regulatórios.
- Automatizar a atualização das instruções de trabalho: eliminando inconsistências e reduzindo erros na manufatura.
- Otimizar o planejamento e execução da produção: garantindo mais eficiência, previsibilidade e melhor aproveitamento dos recursos industriais.
Com uma única plataforma integrada, todos os setores operam de forma sincronizada, promovendo uma manufatura mais ágil, confiável e econômica.
APS3: especialista em transformação digital para a indústria
Garantir a eficiência da engenharia e reduzir custos na produção exige mais do que tecnologia: é preciso contar com um parceiro que entenda os desafios da indústria e saiba como implementar as melhores soluções.
A APS3 é especialista na digitalização de processos industriais e parceira oficial da Siemens, oferecendo consultoria, implantação e suporte do Teamcenter PLM e outras soluções para transformar a gestão de produtos e operações fabris.
Empresas de diversos setores já confiam na APS3 para otimizar seus processos e aumentar sua produtividade.