HERCULES MOTORES TEM MELHORAS DE 63% NO DESEMPENHO DAS ENTREGAS
A Hercules Motores Elétricos, indústria nacional especializada em motores elétricos especiais e inversores de frequência, se destaca no cenário nacional. Com operação iniciada em 2005, hoje já ultrapassaram a marca dos 3 milhões de motores produzidos. Suas instalações fabris ocupam mais de 15.000 m2 e contam com tecnologia de ponta, equipe altamente qualificada, maquinário moderno, laboratórios de pesquisa e controle de qualidade. Ainda, a consciência ambiental, a atenção com a saúde e segurança no trabalho, bem como ações de responsabilidade são marcantes no dia a dia da empresa.
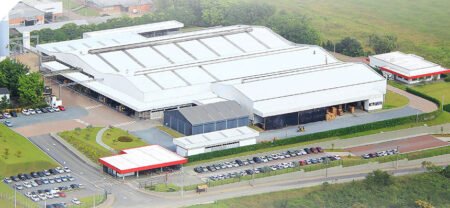
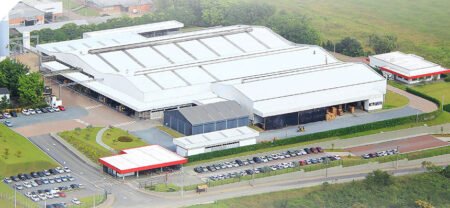
Hoje com uma carteira de aproximadamente 150 clientes mensais, a empresa possui 360 colaboradores no geral e com um faturamento mensal aproximado de 12 milhões.
DESAFIOS
O processo de produção da Hercules Motores é misto, make to order (MTO) e make to stock (MTS), porém, a maior parte é MTO. Atualmente conta com 77 recursos primários divididos em 23 centros de trabalho, cada qual com suas ferramentas e operadores específicos.
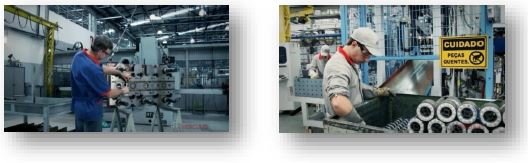
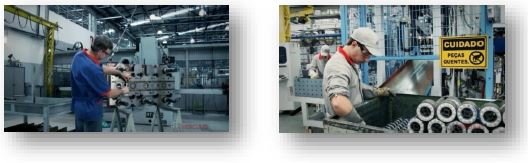
Com o rápido crescimento da Hercules Motores e carência de ferramenta adequada para Planejar, Programar e Controlar o processo produtivo, estavam tendo algumas dificuldades:
- Atraso nas entregas e resposta ao setor de vendas;
- Aceitavam pedidos com datas muito próximas sem considerar a programação atual, gerando transtornos na produção e provocando atrasos nas entregas.
- Meta de 96% das entregas no prazo, porém a Hercules não tinha ferramenta suficiente para planejar o sequenciamento da fábrica, prejudicando o indicador de acuracidade que estava em 58%;
- Dificuldade no sequenciamento das etapas produtivas;
- Dificuldade no controle e otimização de setup;
- Alocação das matérias primas por Ordem de Produção;
- Apontamentos;
- Controle dos componentes PI para cada produto;
- Avaliação dos gargalos devido ao alto mix de produtos;
- Controle das manutenções preventivas;
- Poder de reprogramação em casos de imprevistos.
SOLUÇÃO
Com a instabilidade da programação e as dificuldades existentes no dia a dia da produção, o setor de PPCP procurou uma solução baseada em software fosse capaz de ajudá-los na programação da produção. Neste mesmo período uma das empresas do Grupo Mueller estava implantando com a APS3, Gold Solution Provider localizada em Curitiba/PR, o Preactor para de Programação da Produção. Como parte integrante do Grupo, a Hercules Motores também passou a utilizar como solução o Preactor.
O projeto foi desenvolvido utilizando metodologia SCRUM, tendo o envolvimento de colaboradores dos setores de TI, PPCP, Logística, Produção, Manutenção, vendas, Engenharia de Processos e Produtos.
A Hercules motores utiliza um ERP próprio do Grupo Mueller chamado de Sistema Integrado Mueller (SIM), desenvolvido em GeneXus.
Uma das principais dificuldades na condução do projeto foram os cadastros e a sobrecarga dos recursos humanos.
Para elaboração da solução foram necessárias alterações e a criação de novos cadastros no ERP, além disso, foi necessário rever todos os tempos de processos, criar novos grupos de recursos, levantar todas as ferramentas secundárias e atributos relevantes. Durante o projeto foi identificado que os tempos de setups deveriam ser dependentes de sequencias, então, os recursos foram divididos em 23 centros de trabalhos para gerar matriz de setup a partir de atributos que identificam a troca de característica de produtos.
Com o projeto todos os recursos primários foram sequenciados pelo Preactor, levando em conta 141 restrições secundárias e 170 atributos de setup dependentes de sequencias. As ordens de produção são programadas mensalmente, a reprogramação é diária e o controle de produção é realizado por uma Viewer que o PPCP usa para acompanhar os processos de produção e cobrar os apontamentos do chão de fábrica.
RESULTADOS
Na tabela abaixo constam os objetivos e metas a serem atingidos com o projeto, porém o mais surpreendente foi que logo nos primeiros 4 meses em produção, praticamente todos os resultados dos indicadores foram atingidos.
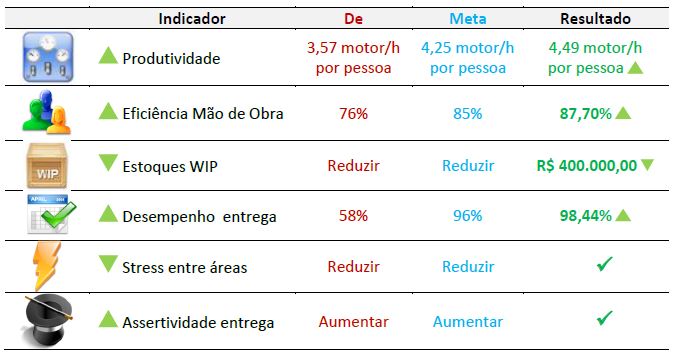
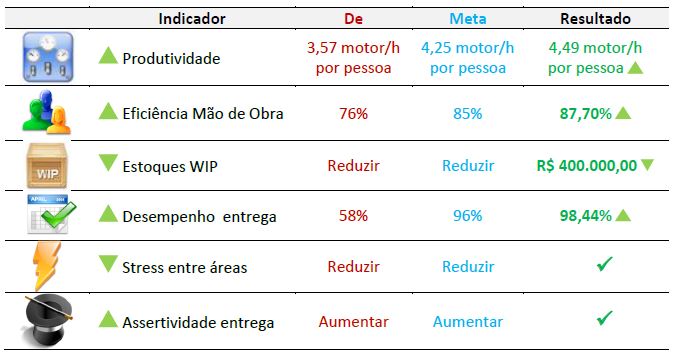
Além dos indicadores previamente registrados, foram percebidas outras melhorias gerais:
- A Área Comercial relatou que reduziu em 70% as ligações dos clientes cobrando posição de seus pedidos atrasados;
- O relacionamento da Área Comercial com a Produção entrou em harmonia, reduzindo drasticamente o “stress”;
- O projeto motivou melhorias no ERP para atender melhor o processo produtivo;
- Redução de um colaborador, pois os trabalhos rotineiros manuais com listagens em planilhas eletrônicas foram reduzidos praticamente em 100%;
- Foi possível internalizar a produção de 80 mil tampas de alumínio que eram terceirizadas;
- O planejamento de compras de matérias primas e estratégicas está sincronizado com a programação, não havendo mais falta de materiais na produção;
- Com o Preactor, a equipe de processo passou a atuar na melhoria da alocação da mão de obra, aproveitando e alocando melhor os recursos disponíveis.