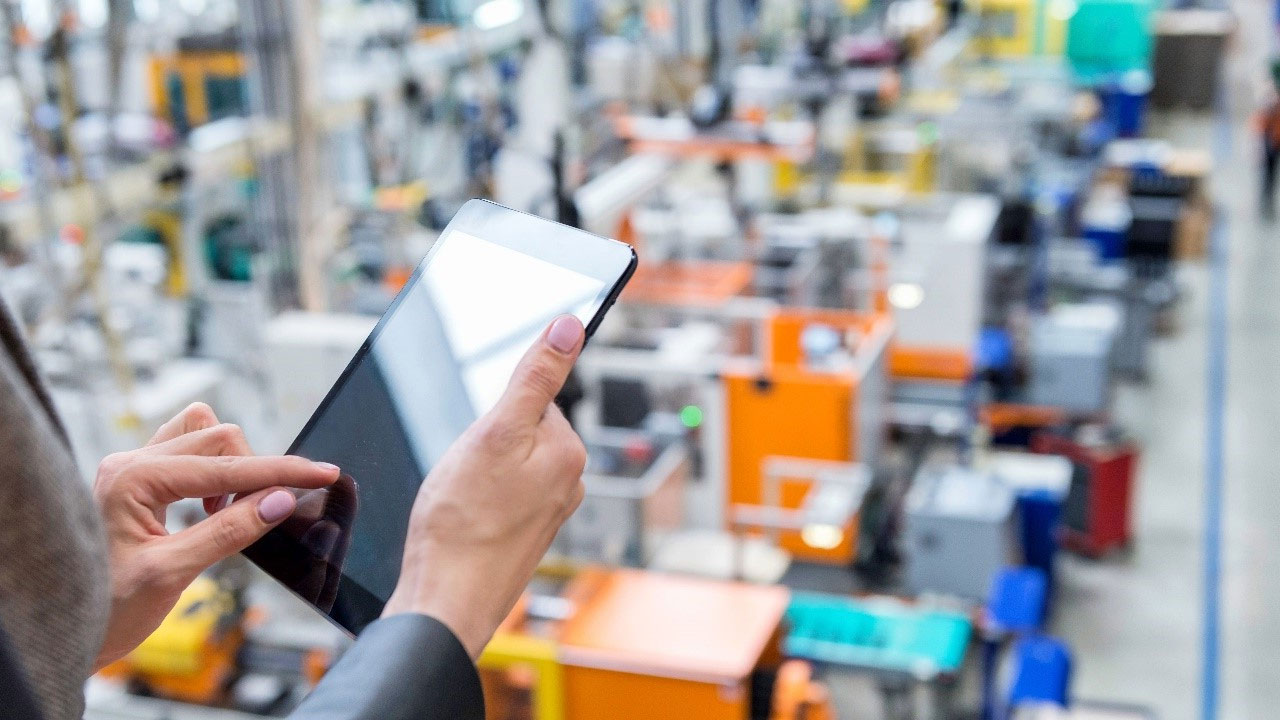
O controle eficiente da produção industrial depende diretamente da capacidade de monitorar e registrar com precisão cada etapa do processo produtivo.
Nesse contexto, o MES (Manufacturing Execution System) se torna uma peça essencial, permitindo a coleta estruturada de dados, o apontamento da produção e o rastreamento de não conformidades.
Ao integrar o MES com sistemas de planejamento avançado, as empresas conseguem alinhar o que foi previsto com o que realmente ocorreu na produção, reduzindo discrepâncias e otimizando processos. O registro preciso dessas informações não apenas melhora a gestão da fábrica, mas também possibilita ajustes estratégicos que aumentam a eficiência e reduzem custos operacionais.
A importância do apontamento de produção
O apontamento de produção refere-se à inserção de dados no sistema sobre a conclusão de ordens de produção. Ele permite que os gestores acompanhem, em tempo real, o desempenho da fábrica e comparem o previsto x realizado, possibilitando análises detalhadas sobre produtividade, eficiência e utilização de recursos.
Sem um registro estruturado, a empresa pode enfrentar desafios como:
- Falta de controle sobre os tempos de produção: sem dados precisos, é difícil identificar gargalos e otimizar o uso de máquinas e mão de obra.
- Dificuldade em prever necessidades de materiais: erros no apontamento podem resultar em excesso de estoque ou falta de insumos, comprometendo a produção.
- Desconexão entre planejamento e execução: sem um fluxo contínuo de informações entre APS e MES, ajustes necessários não são feitos a tempo.
A integração do MES com o APS permite que o planejamento da produção seja ajustado conforme a realidade do chão de fábrica, garantindo maior precisão e alinhamento entre a estratégia e a execução.
Como o MES realiza o apontamento de produção?
O MES atua como um elo entre o chão de fábrica e os sistemas de gestão, automatizando o processo de registro das ordens de produção finalizadas. Ele permite que operadores e gestores tenham acesso a informações detalhadas sobre cada etapa do processo, incluindo:
- Quantidade produzida: monitoramento em tempo real do volume produzido por turno ou máquina.
- Tempos de produção e setup: análise detalhada do tempo gasto em cada etapa, permitindo ajustes para aumentar a eficiência.
- Uso de materiais e insumos: rastreamento de consumo de matéria-prima e comparação com o planejado.
- Paradas não planejadas: identificação de falhas operacionais que impactam a produtividade.
Com essas informações registradas automaticamente, o MES melhora a visibilidade da produção, ajudando os gestores a tomarem decisões mais rápidas e assertivas.
O registro de não conformidades e sua importância
Além do apontamento de produção, o registro de não conformidades é uma das funções mais estratégicas do MES. As não conformidades podem incluir falhas de qualidade, problemas mecânicos, desvios de processo e outras irregularidades que comprometem o desempenho da fábrica.
Rastrear e analisar essas ocorrências é essencial para evitar desperdícios e garantir padrões elevados de qualidade. Algumas razões para dar atenção ao registro de não conformidades incluem:
- Identificação de padrões de falha: ao monitorar onde e quando as falhas ocorrem, é possível identificar causas recorrentes e adotar medidas preventivas.
- Redução de custos com retrabalho e desperdício: corrigir problemas antes que afetem lotes inteiros evita desperdícios e melhora a eficiência.
- Conformidade com normas e certificações: muitas indústrias seguem regulamentações rigorosas e precisam comprovar que possuem um sistema de controle eficaz.
- Melhoria contínua dos processos: entender os problemas de produção permite ajustes que aumentam a produtividade e reduzem riscos.
Por exemplo, em uma indústria automotiva, o MES pode registrar falhas em peças produzidas e correlacioná-las a lotes específicos de matéria-prima. Isso permite identificar rapidamente fornecedores problemáticos e evitar que produtos defeituosos cheguem ao mercado.
A integração do MES com sistemas de planejamento
O MES sozinho já oferece ganhos significativos para a gestão da produção, mas sua eficiência aumenta ainda mais quando integrado a soluções como o APS. Enquanto o MES coleta e organiza os dados operacionais em tempo real, o APS utiliza essas informações para otimizar o planejamento e o sequenciamento da produção.
Benefícios dessa integração:
1. Melhor alinhamento entre planejamento e execução: os ajustes no plano de produção podem ser feitos de forma dinâmica, evitando perdas.
2. Redução de tempos de inatividade: ao antecipar gargalos e falhas, é possível minimizar impactos e melhorar a utilização da capacidade produtiva.
3. Otimização da alocação de recursos: com dados precisos sobre a produção real, o APS pode recalcular ordens e ajustar prioridades.
4. Maior previsibilidade na tomada de decisões: informações atualizadas possibilitam decisões mais estratégicas sobre produção, compras e logística.
Com a combinação de MES + APS, as indústrias conseguem um controle muito mais refinado da sua operação, resultando em maior produtividade e competitividade no mercado.
Opcenter X: modernizando a gestão da produção
O Opcenter X, desenvolvido pela Siemens, é uma solução modular 100% em nuvem voltada para a Gestão de Operações de Fabricação (MOM/MES). Ele permite que indústrias de pequeno e médio porte tenham acesso a uma plataforma poderosa para controle e otimização da produção.
Entre os principais benefícios do Opcenter X, destacam-se:
- Automação do apontamento de produção: coleta de dados em tempo real, reduzindo falhas humanas e melhorando a precisão dos registros.
- Gestão de não conformidades: rastreamento detalhado de falhas e implementação de ações corretivas.
- Integração com APS e ERP: conexão entre planejamento, execução e finanças para um fluxo de produção mais eficiente.
- Implementação rápida e escalável: solução baseada em nuvem que permite um crescimento gradual conforme a necessidade da empresa.
Muito além do MES
O Opcenter X abrange mais do que o controle de produção. Seus módulos incluem:
- Engenharia: Criação de dados de engenharia, planejamento do processo de fabricação e modelagem de fábrica.
- Gerenciamento de pedidos: Integração com ERP para importação de listas, atribuição de processos e lançamento de pedidos em produção.
- Execução: Gerenciamento de ordens de serviço, rastreamento de materiais e coleta de dados em tempo real.
- Qualidade: Registro de não conformidades, execução de inspeções e gerenciamento de falhas e medidores.
- Sequenciamento: Sequenciamento automático de ordens baseado na disponibilidade de equipamentos.
- Relatórios e painéis: Monitoramento de usuários, diagnósticos e direitos de acesso.
APS3: liderança em transformação digital
A APS3 é pioneira na implementação do Opcenter X na América do Sul. Com experiência prática e atualização constante, nossa equipe entrega soluções de excelência para transformar digitalmente as operações industriais. Além de oferecer suporte local e desenvolvimento global, promovemos inovações sustentáveis e parcerias de longo prazo.
Se sua empresa busca uma solução para alavancar sua gestão de produção, clique aqui e conheça mais sobre o Opcenter X.