HERCULES MOTORS IMPROVE DELIVERY PERFORMANCE BY 63%
As a result of investments that have enabled the company to have a modern industrial and highly competitive plant, Hercules Electric Motors Ltda., which specializes in the production of electric motors and special frequency inverters, began operating in 2005. During this period the milestone of three million motors produced was exceeded. Hercules Electric Motors came to the market with some differentiators, the plant, which occupies an area of more than 15,000 m2, houses modern equipment, highly trained personnel and research laboratories, and a Total Quality Control system, which is completely in tune with the market place requirements. Complementing this, the company also implements sustainability initiatives and constantly maintains controls to issues such as health, safety and environmental awareness.
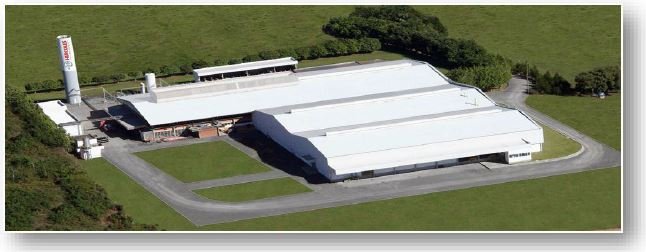
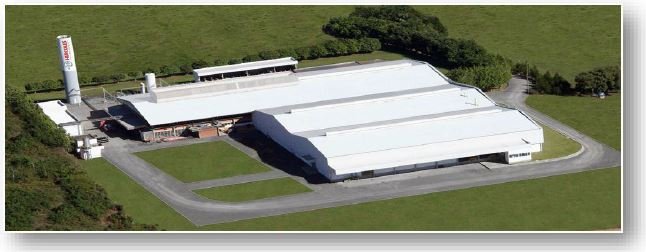
Today, with a portfolio of approximately 150 clients per month, the company has 360 employees and a monthly turnover of approximately US$12 million.
CHALLENGE
The production process of Hercules Motors is mixed, with make-to-order (MTO) and make-to-stock (MTS) production orders, but mostly MTO. Currently it has 77 primary resources divided into 23 work centres, each with its specific tools and operators.
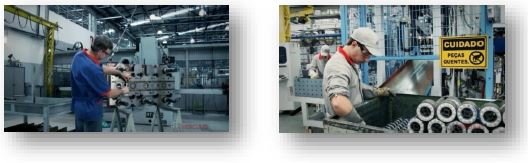
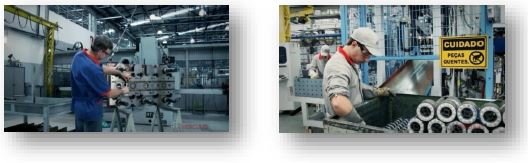
With the rapid growth of the Hercules Motors and lack of an appropriate tool for Planning, Scheduling and Controlling in the production process, they were having some difficulties:
- Delay in deliveries and responses to the sales department;
- They accepted orders with very short turnaround dates without considering the current schedule, causing confusion in the production department and causing delays in deliveries;
- There was a planned target of 96% for on-time deliveries, but Hercules did not have enough time to plan the sequencing of the factory, the actual achieved rate could be calculated at 58% for on-time deliveries;
- Difficulty in sequencing the production stages;
- Difficulty in controlling and optimizing setups;
- Allocation of raw materials for production orders;
- Production controls;
- Management of components for each product;
- Creation of bottlenecks due to the high product mix;
- Management of preventive maintenance;
- Hability to reschedule after unforeseen events
SOLUTION
With the instability of the program and the difficulties in day to day production, the PP&C sector sought a software-based solution to be able to help them with the production schedules. During the same period another Mueller Group company was implementing Preactor for Production Scheduling in partnership with APS3, Gold Solution Provider located in Curitiba / PR. As part of the Group, Hercules Motors also began to use the Preactor solution.
The project was developed using SCRUM methodology, with the involvement of employees of IT, PP&C, Logistics, Manufacturing, Maintenance, Sales, Engineering Processes and Products sectors.
Hercules Motors uses an ERP system of the Mueller’s own group called Integrated Mueller (SIM), developed in GeneXus.
One of the major difficulties in conducting the project was the number of records to be processed and the labour intensive work needed to convert the data.
To implement the solution, it was necessary to make changes and create new entries into the ERP system. Moreover, it was necessary to review all the process times, create new groups of resources, and raise all the secondary tools and their relevant attributes. During the project it was assessed that the setup times should be sequence dependant. The resources were divided into 23 work centres to generate a setup matrix by using the attributes that identify the different product features.
Within the project all primary resources were scheduled by Preactor, taking into account 141 secondary constraints and 170 sequence dependent setup attributes. The production orders are scheduled monthly, reprogramming is done on a daily basis and production control is performed by a Viewer that PP&C uses to monitor production processes and collect data from the factory floor.
RESULTS
The table below displays the goals and objectives to be achieved in the project, but more surprising was that in the first four months in use, virtually all of the indicators achieved the desired results.
In addition to the indicators previously recorded, other general improvements were achieved:
- The Business Area reported a reduction of 70% in customers chasing their overdue orders;
- The relationship between the Commercial Area and Production entered into a state of harmony, dramatically reducing the “stress” between them;
- The project led to improvements in the ERP system to better serve the whole production process;
- Reduction of employee idle time during the routine manual work with spreadsheet lists reduced almost 100%;
- It was possible to internalize the production of 80,000 aluminium lids that were previously outsourced;
- The purchase planning of strategic and raw materials is synchronized with the schedule, with no more material shortages in production;
- With Preactor, the process team started to work on improving the allocation of labour, as well as taking advantage of and allocating the available resources.