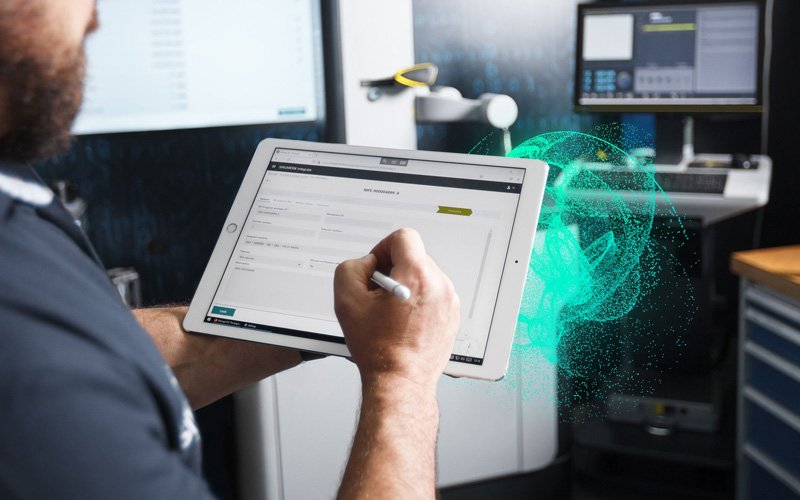
Nos últimos anos, a indústria tem enfrentado desafios crescentes devido à necessidade de produzir lotes menores e mais customizados, seguindo as demandas de mercados cada vez mais segmentados.
Um dos principais obstáculos nesse contexto é a frequência e o tempo dos setups — a preparação de máquinas para diferentes processos de produção. Reduzir o tempo de setup é essencial para melhorar a eficiência operacional e a competitividade das empresas. Neste artigo, discutiremos técnicas e ferramentas eficazes para a redução de setups na produção e como o Opcenter APS da Siemens pode ser uma solução valiosa nesse processo.
Importância da redução de setups
Reduzir o tempo de setup é fundamental para maximizar a capacidade produtiva e minimizar os tempos improdutivos nas linhas de produção. Em um cenário onde a produção em massa deu lugar a lotes menores e mais diversificados, a agilidade na troca de ferramentas e na configuração de máquinas se tornou vital. A redução de setups não só diminui o tempo ocioso das máquinas, como também permite uma resposta mais rápida às mudanças de demanda do mercado.
Agrupamento de ordens com características semelhantes
Uma das técnicas mais eficazes para reduzir o tempo de setup é agrupar ordens de produção com características semelhantes. Isso significa organizar a produção de forma que itens com requisitos similares sejam fabricados consecutivamente. Ao fazer isso, é possível minimizar as alterações necessárias nos equipamentos, reduzindo assim o tempo gasto em setups.
Por exemplo, se uma fábrica de embalagens produz diferentes tipos de caixas de papelão, agrupar a produção de caixas de tamanhos semelhantes pode evitar a necessidade de ajustar as máquinas entre cada lote. Esse agrupamento não apenas economiza tempo, mas também reduz o desgaste das máquinas e a necessidade de ajustes frequentes.
Na imagem à esquerda, o gráfico mostra o percentual de utilização da máquina durante o período considerado. Estão programadas seis ordens de produção, divididas igualmente entre vermelhas, verdes e azuis. As barras pretas indicam os tempos de setup necessários para a troca de cores dos itens.
Na imagem à direita, as ordens de produção com produtos da mesma cor foram agrupadas, permitindo um melhor aproveitamento do setup. Isso resultou em uma liberação de capacidade da máquina, aumentando a eficiência operacional.
Ferramentas de capacidade finita
Outra estratégia importante é a utilização de ferramentas de capacidade finita. Essas ferramentas permitem que as empresas planejem e programem suas operações com base na capacidade real dos recursos disponíveis, em vez de usar uma abordagem genérica de capacidade infinita. Isso significa levar em consideração os limites reais de máquinas, mão de obra e outros recursos, permitindo um planejamento mais preciso e eficaz.
Com ferramentas de capacidade finita, é possível identificar gargalos na produção e ajustar os sequenciamentos para maximizar a eficiência. Por exemplo, se uma máquina específica é um ponto crítico no processo de produção, a ferramenta pode ajudar a programar a produção de modo a minimizar o tempo de inatividade e otimizar o uso desse recurso.
Técnicas de otimização de produção
Para otimizar a produção e reduzir o tempo de setup, é essencial adotar uma abordagem abrangente que considere toda a cadeia de produção. Vamos explorar como essas técnicas funcionam na prática.
A abordagem tradicional:
Em muitas empresas, a otimização é feita de forma individual por setor, sem considerar a linha de produção como um todo. Isso pode levar a uma falta de sincronização, onde um setor está pronto para operar enquanto outro está realizando um setup, causando ineficiências no processo global. Por exemplo, uma fábrica pode organizar a produção de modo que cada setor esteja operando na sua capacidade máxima, mas sem considerar os setups entre diferentes setores, resultando em tempos de inatividade desnecessários.
A abordagem APS:
Com ferramentas de APS (Advanced Planning and Scheduling), a otimização é realizada para toda a cadeia de produção. O sistema considera a sequência ideal de produção, minimizando o tempo total de setup ao longo de toda a linha. Por exemplo, se a produção requer mudanças de cor frequentes, o APS pode agrupar as ordens de produção de modo que as cores semelhantes sejam produzidas consecutivamente, reduzindo os setups e aumentando a eficiência.
Decisão baseada em cenários:
Uma das grandes vantagens do APS é a capacidade de simular diferentes cenários de produção. Isso permite às empresas escolher entre cenários com menos setups, que podem levar a algumas ordens atrasadas, ou cenários com mais setups, mas que garantem que todas as entregas estejam no prazo. Essa flexibilidade permite que as empresas ajustem suas operações conforme as prioridades do momento, seja para minimizar custos ou maximizar a pontualidade das entregas.
Como o Opcenter APS da Siemens pode ajudar
O Opcenter APS (Advanced Planning and Scheduling) da Siemens é uma ferramenta poderosa que pode ajudar as empresas a implementar essas técnicas de maneira eficaz. Ele oferece uma plataforma integrada para planejamento e programação avançada, permitindo que as empresas otimizem seus processos de produção e reduzam o tempo de setup.
Planejamento e programação avançada
Com o Opcenter APS, as empresas podem criar sequenciamentos detalhados que consideram a capacidade real dos recursos disponíveis. Isso permite uma programação mais precisa e evita surpresas no chão de fábrica. A ferramenta também facilita o ajuste dinâmico dos sequenciamentos com base em mudanças nas demandas ou na disponibilidade dos recursos.
Visibilidade e controle
O Opcenter APS proporciona visibilidade completa sobre o processo de produção, permitindo que os gestores identifiquem rapidamente gargalos e tomem ações corretivas. Com informações em tempo real sobre a produção, é possível ajustar os sequenciamentos e as prioridades de forma ágil, garantindo que os recursos sejam utilizados da maneira mais eficiente possível.
Simulação de cenários
Uma das funcionalidades mais valiosas do Opcenter APS é a capacidade de simular diferentes cenários de produção. Isso permite que as empresas testem várias estratégias de setup e programação antes de implementá-las, identificando a abordagem mais eficaz para reduzir o tempo de setup e otimizar a produção.
Integração com outras soluções
O Opcenter APS pode ser integrado com outras soluções de software e sistemas existentes na empresa, criando uma plataforma coesa para a gestão de operações. Isso facilita a troca de informações e a coordenação entre diferentes departamentos, melhorando a eficiência geral da produção.
APS3: expertise em soluções para redução de setups
Implementar técnicas e ferramentas para reduzir setups pode transformar a eficiência operacional da sua empresa. A APS3 é a parceira ideal para ajudar sua organização a implementar o Opcenter APS da Siemens de maneira eficaz. Com uma equipe especializada e vasta experiência em diagnósticos e implementação de soluções avançadas, a APS3 está pronta para auxiliar sua empresa a alcançar novos níveis de produtividade.
Clique aqui e descubra como o Opcenter APS pode revolucionar a gestão de operações de manufatura da sua empresa. Explore as possibilidades de transformar suas operações com tecnologia de ponta e conte com o suporte de especialistas dedicados ao sucesso da sua empresa. |