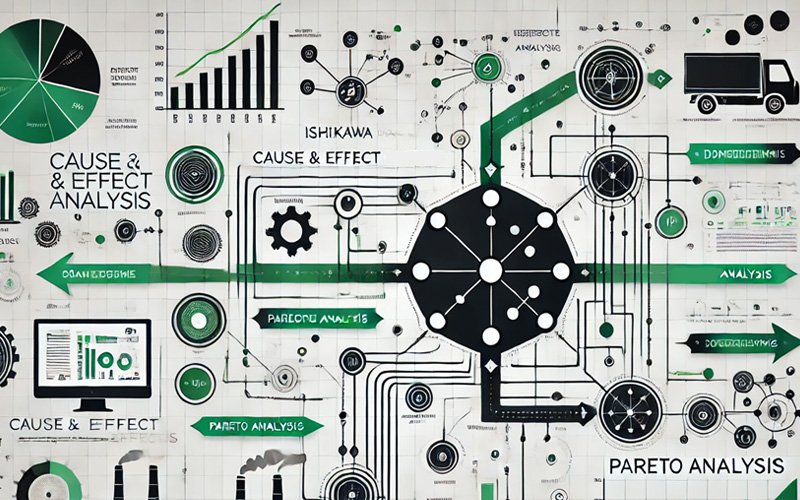
No ambiente industrial, a capacidade de tomar decisões informadas é essencial para a eficiência e competitividade.
Um método fundamental para aprimorar essa capacidade é a análise de causa e efeito, uma abordagem sistemática que visa identificar, entender e resolver problemas, permitindo que as empresas tomem decisões mais informadas e eficazes. No contexto da produção industrial, essa análise é essencial para melhorar a eficiência, a qualidade e a produtividade.
O que é a análise de causa e efeito?
A análise de causa e efeito, também conhecida como análise de causa-raiz, é um método que busca identificar as causas subjacentes de um problema. Ao invés de tratar apenas os sintomas, essa análise foca em encontrar a raiz do problema para evitar sua recorrência. Isso é particularmente importante na produção industrial, onde problemas podem causar interrupções significativas e impactar negativamente os resultados.
Métodos e ferramentas utilizadas na análise de causa e efeito
Existem várias ferramentas e métodos que facilitam a análise de causa e efeito. Entre as mais populares estão o diagrama de Ishikawa e a análise de Pareto.
Diagrama de Ishikawa (Espinha de Peixe)
O Diagrama de Ishikawa, também conhecido como Diagrama de Espinha de Peixe ou Diagrama de Causa e Efeito, é uma ferramenta visual que ajuda a identificar, explorar e ilustrar todas as causas potenciais de um problema específico.
A aparência do diagrama lembra a estrutura óssea de um peixe, onde a “cabeça” representa o problema ou efeito a ser investigado. As “espinhas” principais que se ramificam da espinha dorsal simbolizam categorias amplas de causas, como mão de obra, método, máquina, material, meio ambiente e medida.
Cada uma dessas categorias é, então, dividida em subcausas menores, criando uma visão detalhada de todas as possíveis influências sobre o problema. Essa visualização detalhada permite uma análise minuciosa, ajudando a identificar áreas específicas que necessitam de intervenção.
Análise de Pareto
A análise de Pareto é baseada no princípio de Pareto, também conhecido como a regra 80/20, que sugere que aproximadamente 80% dos efeitos vêm de 20% das causas. Em outras palavras, a maioria dos problemas geralmente é causada por um pequeno número de fatores. Utilizando gráficos de Pareto, as empresas podem priorizar as causas mais significativas e focar seus esforços naquelas que terão o maior impacto na melhoria da produção. Isso permite uma abordagem mais eficiente e direcionada na resolução de problemas.
Como essas ferramentas ajudam a identificar problemas potenciais
Prevenção proativa
análise de causa e efeito é a capacidade de identificar problemas potenciais antes que eles ocorram. Isso permite que as empresas tomem medidas preventivas, evitando interrupções na produção e garantindo a continuidade operacional. A identificação precoce de problemas também reduz custos associados a retrabalho, desperdício de materiais e paradas de máquinas.
Melhoria contínua
A utilização regular dessas ferramentas promove uma cultura de melhoria contínua dentro da organização. Ao analisar consistentemente as causas dos problemas e implementar soluções eficazes, as empresas podem aprimorar seus processos e aumentar a eficiência ao longo do tempo. Isso não só melhora a produção, mas também contribui para a satisfação do cliente ao entregar produtos de qualidade superior.
Tomada de decisões informadas
Com uma análise detalhada das causas e efeitos, os gestores de produção podem tomar decisões mais informadas. Em vez de basear-se em suposições ou dados incompletos, a análise de causa e efeito fornece uma base sólida para a tomada de decisões estratégicas. Isso resulta em ações mais eficazes e na implementação de melhorias que realmente fazem a diferença.
Como o Opcenter APS facilita a análise de causa e efeito
O Opcenter APS da Siemens é uma solução poderosa que complementa as ferramentas mencionadas anteriormente, facilitando a análise de causa e efeito na produção. Com ferramentas gráficas e inteligentes, ele permite uma visualização clara e detalhada das operações, ajudando na identificação de problemas e na gestão de desvios.
Ferramentas gráficas
O Opcenter APS proporciona gráficos intuitivos que permitem uma visualização clara dos dados de produção. Esses gráficos facilitam a identificação de tendências e padrões, tornando mais fácil detectar as causas subjacentes dos problemas. Além disso, a capacidade de simular diferentes cenários de produção permite que os gestores avaliem o impacto de possíveis soluções antes de implementá-las.
Gestão de desvios
Com o Opcenter APS, as empresas podem monitorar e gerir desvios em tempo real. Isso inclui a identificação rápida de problemas e a implementação de ações corretivas imediatas. A capacidade de rastrear desvios ao longo do tempo também ajuda a identificar causas recorrentes e a desenvolver estratégias para evitá-las no futuro.
Integração de dados
A integração de dados proporcionada pelo Opcenter APS permite uma análise abrangente e holística das operações de produção. Ao combinar dados de diferentes fontes, a ferramenta oferece uma visão completa do processo produtivo, facilitando a identificação de causas e efeitos complexos que podem não ser evidentes com uma análise mais limitada.
APS3: Seu parceiro na implementação do Opcenter APS
A APS3, em parceria com a Siemens, é especializada no diagnóstico e implementação do Opcenter APS. Com uma equipe altamente capacitada e um enfoque centrado nas necessidades do cliente, a APS3 oferece soluções inovadoras que ajudam as empresas a otimizar suas operações de produção.
Com a APS3, você terá um parceiro confiável para implementar o Opcenter APS de forma eficaz, transformando sua análise de causa e efeito e melhorando significativamente a tomada de decisões na produção.
Clique aqui para saber mais sobre como a APS3 pode ajudar sua empresa a enfrentar os desafios da produção e implementar o Opcenter APS.