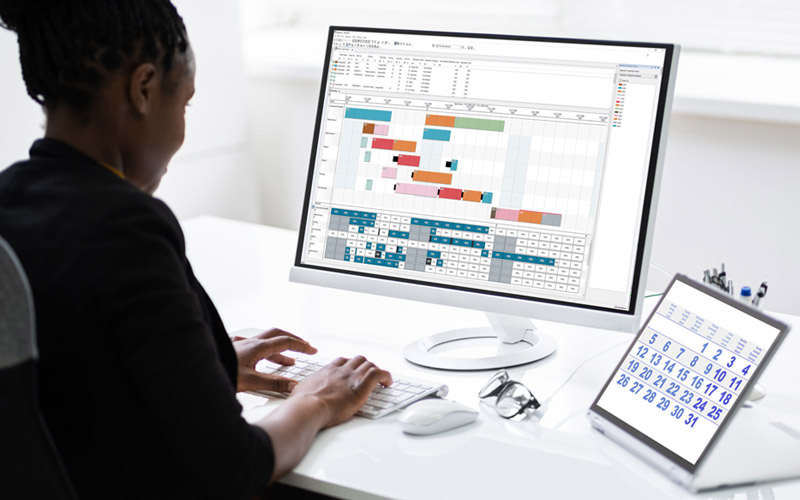
A transformação digital na indústria é um tópico em alta, e duas soluções tecnológicas desempenham um papel crucial nesse cenário: o Sistema de Planejamento Avançado e Programação (APS) e o Gerenciamento do Ciclo de Vida do Produto (PLM).
Embora essas soluções sejam frequentemente vistas como distintas e voltadas para setores diferentes dentro de uma indústria, a verdade é que elas são altamente complementares. Este artigo explora a conexão entre o Teamcenter (PLM) e o Opcenter APS, ambos da Siemens, e como essa integração pode otimizar todo o ciclo de vida do produto.
Importância da conexão na indústria digital
À medida que a indústria avança na era digital, a necessidade de uma integração eficaz entre diferentes sistemas e setores torna-se cada vez mais evidente. Não se trata apenas de coletar dados, mas de como esses dados são compartilhados, interpretados e utilizados para tomar decisões informadas.
A ideia de ter uma “fonte única da verdade” é muito importante na indústria digital. Em vez de ter informações espalhadas em diferentes lugares, tudo fica guardado em um único sistema ou em sistemas que se falam entre si. Isso é o que chamamos de “digitalização em circuito fechado”.
Mas essa digitalização vai além de apenas automatizar coisas. Ela conecta e alinha todos os setores da indústria, do começo ao fim do ciclo de vida do produto. Isso faz com que todas as informações sejam atualizadas e confiáveis em tempo real. Assim, não é preciso perder tempo checando ou corrigindo dados em diferentes sistemas, o que diminui as chances de erros (saiba mais sobre os conceitos de gêmeos digitais e trilhas digitais neste artigo).
Da Engenharia ao Chão de Fábrica
Design do Produto e Lista de Materiais (BOM)
Os primeiros passos na criação de qualquer produto são a ideação e o projeto, que geralmente são realizados por engenheiros e projetistas com o auxílio de ferramentas CAD. A lista de materiais (BOM, do inglês Bill of Materials) é gerada neste estágio e é essencial para entender quais materiais são necessários para a fabricação do produto.
Contudo, a construção inicial da BOM, feita pela engenharia de produto, nem sempre condiz com a lógica de fabricação do produto. Portanto, o Teamcenter trabalha com a possibilidade de variações da BOM. Nesse artigo, exemplificamos a EBOM e a MBOM.
EBOM: costuma ser a primeira BOM do produto e é estruturada sob a perspectiva do departamento de engenharia de produto. A estruturação costuma contar com agrupamentos por função, tipo de sistema, entre outros. Como exemplo, podemos ter uma EBOM com submontagens do tipo: motor 1; motor 2; bateria 1, etc.
MBOM: deriva da EBOM e possui estrutura voltada para o processo fabril. Ou seja, para o mesmo produto citado, as submontagens poderiam ser: estação 1; estação 2; torno 1, etc.
O Teamcenter PLM estabelece uma conexão “de-para” entre a EBOM e a MBOM. Desta forma, cada setor poder visualizar o formato que mais se adeque à sua realidade. Ainda, vale ressaltar que alterações realizadas no produto pela engenharia de produto (EBOM), tais como revisão de peça, inclusão de anexos, entre outros, são carregadas para a MBOM, e vice-versa.
Roteiros de Fabricação (BOP)
Após estruturar as listas de materiais, a atenção se volta para a elaboração dos roteiros de fabricação, comumente designados como Bill of Process (BOP). Utilizando o Teamcenter (PLM), engenheiros de processo tomam a BOM como base para desenvolver uma sequência de operações alinhada com as necessidades da produção. A BOP serve como um manual abrangente, detalhando a sequência, as máquinas/processos e o tempo estimado para cada operação no ciclo de fabricação.
Entrada de Dados no ERP
O sistema de Planejamento de Recursos Empresariais (ERP) atua como um repositório central, onde as informações cruciais como BOM e BOP são armazenadas e integradas. Neste estágio, o ERP, muitas vezes em colaboração com o Teamcenter (PLM), é responsável por emitir as ordens de produção que serão fundamentais para a fase de planejamento e programação do Opcenter APS.
Planejamento e Programação com APS
O Opcenter APS entra em cena como um otimizador de produção, utilizando os dados provenientes do ERP para elaborar planos de produção altamente eficientes. O APS avalia uma série de variáveis e restrições, incluindo a disponibilidade de materiais e a capacidade das máquinas, para gerar cenários de produção que maximizam a eficiência e a eficácia do processo produtivo.
Produção
Na etapa final de produção, o Opcenter APS atua como um guia estratégico no chão de fábrica, otimizando a sequência de operações e a alocação de recursos. Além de planejar, o APS eleva sua funcionalidade ao simular cenários de produção em tempo real, oferecendo aos gestores a capacidade de selecionar a estratégia mais alinhada com as necessidades e realidades específicas da empresa. Adicionalmente, o Teamcenter pode ser utilizado para criação de instruções de trabalho (ITs) vinculadas às informações do produto. Com isso, mudanças são propagadas e atualizam automaticamente as ITs, além de fornecer recursos visuais para o operador e estarem conectadas às estruturas criadas (EBOM, MBOM e BOP).
Dessa forma, o Teamcenter PLM e o Opcenter APS trabalham em harmonia, desde a concepção do produto até sua fabricação, garantindo um processo integrado e eficiente em todas as etapas.
Descubra mais com a APS3
Se a ideia de transformar digitalmente sua operação industrial ressoa com você, a APS3 está aqui para ser seu parceiro nessa jornada. Em nosso site, você encontrará informações detalhadas sobre como cada uma dessas soluções pode ser adaptada às necessidades específicas da sua empresa.
Não apenas fornecemos ambas as soluções, como também oferecemos consultoria especializada para garantir que sua implementação seja bem-sucedida. Estamos comprometidos em ajudar sua empresa a atingir novos patamares de eficiência e competitividade no cenário digital atual.