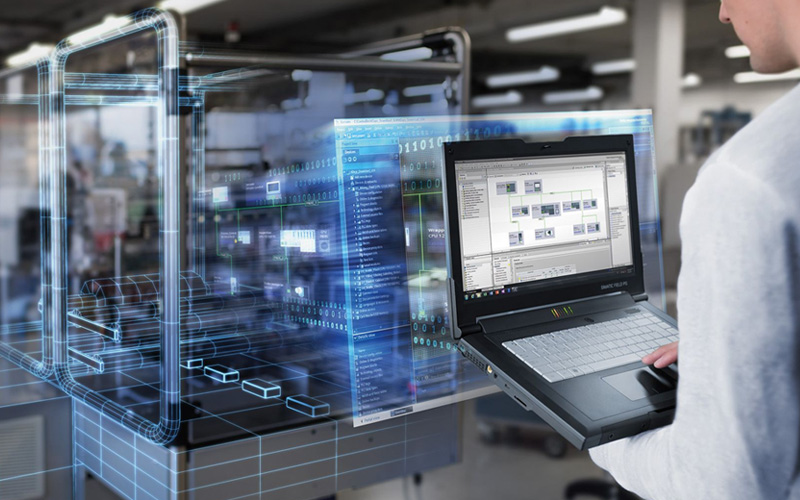
Nas operações industriais, o PPCP (Planejamento, Programação e Controle da Produção) e o chão de fábrica são como dois lados da mesma moeda.
Enquanto o PPCP organiza as demandas e planeja as atividades, o chão de fábrica transforma esses planos em realidade. No entanto, quando os dados não fluem entre essas áreas de maneira integrada, os efeitos podem ser desastrosos: excesso de estoques, rupturas no abastecimento e até dificuldades para atender pedidos dentro do prazo. A solução? Uma execução colaborativa baseada na integração de dados em tempo real.
Os desafios da falta de integração
Um dos maiores obstáculos na gestão de produção é o desalinhamento entre o que o PPCP planeja e o que realmente acontece no chão de fábrica. Imagine uma linha de produção que deveria fabricar 500 unidades de um componente, mas, devido a falhas no abastecimento, só consegue produzir 300. O PPCP, sem acesso a essa informação em tempo real, continua planejando como se as 500 unidades estivessem disponíveis. O resultado? Atrasos em pedidos, aumento de estoque de produtos inacabados e insatisfação dos clientes.
A falta de comunicação efetiva entre essas áreas cria um efeito cascata de problemas. Por exemplo:
- Estoque excessivo: quando o PPCP não tem visibilidade sobre as necessidades reais, a tendência é planejar produção ou compras além do necessário.
- Rupturas de abastecimento: o contrário também acontece: a falta de dados atualizados pode gerar escassez de insumos, interrompendo a produção.
- Desperdício de tempo e recursos: replanejamentos frequentes, retrabalho e setups desnecessários tornam a operação menos eficiente.
- Decisões baseadas em achismos: sem informações confiáveis, as decisões se tornam reativas, com maior risco de erros.
Esses desafios não são raros, especialmente em fábricas que ainda dependem de processos manuais ou sistemas desconectados.
Execução colaborativa: o poder da integração de dados
A execução colaborativa surge como uma solução poderosa para conectar o PPCP ao chão de fábrica. Trata-se de integrar registros, relatórios e dados em tempo real, criando uma visão única para todas as áreas envolvidas. Com isso, as decisões deixam de ser baseadas em estimativas ou informações atrasadas, tornando-se mais assertivas e rápidas.
Imagine um cenário em que o chão de fábrica registra automaticamente qualquer interrupção ou ajuste na produção, e essa informação é instantaneamente compartilhada com o PPCP. Esse nível de transparência permite que ajustes sejam feitos no planejamento sem comprometer o fluxo produtivo ou os prazos de entrega.
Benefícios da execução colaborativa
Adotar uma abordagem colaborativa traz benefícios significativos para a gestão industrial:
- Redução de estoques excessivos: dados precisos sobre o que foi produzido ajudam a alinhar os níveis de estoque às necessidades reais.
- Melhoria no fluxo produtivo: com a visibilidade em tempo real, gargalos podem ser identificados e resolvidos rapidamente.
- Agilidade nas decisões: informações atualizadas permitem ajustes imediatos nos planos de produção e compras.
- Maior engajamento das equipes: a integração promove uma comunicação mais fluida, reduzindo conflitos e aumentando a confiança entre setores.
- Atendimento mais eficiente às demandas: com dados confiáveis, a capacidade de atender pedidos no prazo aumenta significativamente.
Exemplo prático: como a integração transforma operações
Em uma fábrica de componentes eletrônicos, o PPCP costumava planejar ordens de produção com base em dados de semanas anteriores. Certo dia, um defeito em uma máquina interrompeu a produção de um lote crítico, mas a informação só chegou ao PPCP no final do dia seguinte. O resultado foi um atraso na entrega, já que a programação da produção não foi ajustada a tempo.
Após implementar soluções integradas, o chão de fábrica passou a registrar automaticamente todas as ocorrências no sistema, permitindo que o PPCP fosse informado em tempo real. Quando outra falha ocorreu, o PPCP reprogramou a produção imediatamente, utilizando um roteiro alternativo para finalizar o lote. Dessa vez, o pedido foi entregue no prazo, e a empresa evitou penalidades e insatisfação do cliente.
Soluções digitais para uma execução colaborativa eficaz
O avanço da tecnologia tornou possível integrar dados em tempo real entre o PPCP e o chão de fábrica de maneira eficiente e acessível. Ferramentas como o Opcenter APS e o Opcenter X, da Siemens, são fundamentais para promover essa conexão.
Opcenter APS: planejamento estratégico e programação precisa
- Planejamento estratégico com o módulo Planning: ideal para decisões de médio e longo prazo, o Opcenter APS Planning utiliza previsões de demanda e ordens de produção para criar planos gerais que alinham capacidades e recursos disponíveis.
- Programação detalhada com o módulo Scheduling: focado no curto prazo, o Opcenter APS Scheduling fornece sequências precisas para a produção, reprogramando automaticamente diante de mudanças ou interrupções no chão de fábrica.
Opcenter X: visibilidade e controle em tempo real
- Gerenciamento de ordens de serviço: controle eficiente de cada etapa da produção, desde a entrada do pedido até sua conclusão.
- Rastreamento em tempo real: monitore materiais e operações diretamente no chão de fábrica.
- Qualidade garantida: gerencie não conformidades, análises de falhas e execução de inspeções.
Resultados que vão além da eficiência operacional
Essas soluções trabalham em sinergia para garantir que o PPCP e a fábrica estejam sempre alinhados, possibilitando que as indústrias alcancem melhorias que impactam diretamente os resultados financeiros e a satisfação dos clientes. Estoques otimizados, redução de custos com setups e maior previsibilidade na produção resultam em uma operação mais enxuta e competitiva. Além disso, a possibilidade de ajustar rapidamente o planejamento e a programação, permitem uma resposta mais ágil às mudanças do mercado.
Transformando desafios em oportunidades
Empresas que adotam uma abordagem colaborativa e integram seus dados de produção conseguem transformar desafios em vantagens competitivas. Além de melhorar a eficiência operacional, essa prática cria um ambiente de trabalho mais harmônico, onde todos os setores trabalham com os mesmos objetivos e informações confiáveis.
Na APS3, ajudamos indústrias de diversos segmentos a implementar soluções como o Opcenter APS e o Opcenter X, promovendo integração, eficiência e resultados consistentes.
Quer saber como conectar seu PPCP ao chão de fábrica e tomar decisões mais inteligentes? Conheça nossas soluções em:
APS3 – Opcenter APS
APS3 – Opcenter X