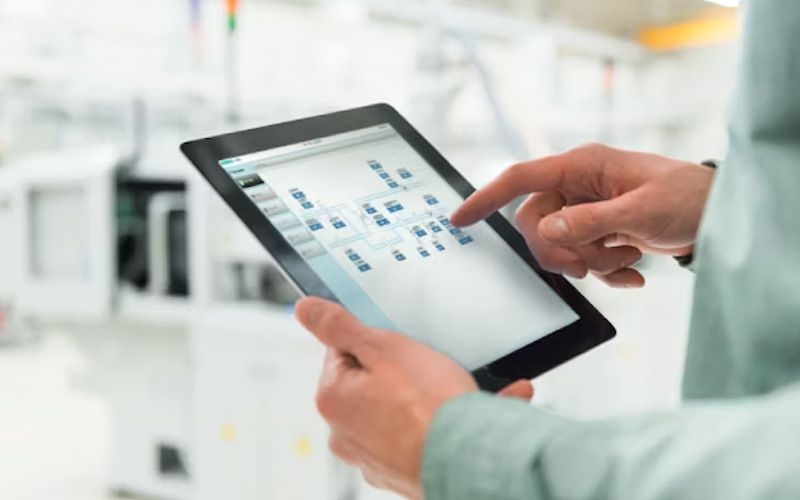
No coração das operações industriais, o Plano Mestre da Produção (PMP), também conhecido como Master Production Schedule (MPS), é responsável por alinhar demandas do mercado, capacidade produtiva e disponibilidade de materiais.
Ele funciona como um guia estratégico que direciona a produção para atender prazos, garantir eficiência e evitar desperdícios. Contudo, quando elaborado sem critérios adequados, o PMP pode gerar mais problemas do que soluções, impactando diretamente os resultados operacionais e financeiros da empresa.
O que caracteriza um PMP de baixa qualidade?
Um PMP de baixa qualidade frequentemente reflete planejamento desalinhado com a realidade operacional da empresa. Um exemplo clássico é a utilização de uma abordagem de “capacidade infinita”, que ignora as limitações reais da fábrica, como disponibilidade de máquinas, mão de obra e materiais. Além disso, a ausência de atualizações regulares no plano resulta em cronogramas desatualizados, que não acompanham mudanças no mix de produtos ou na demanda.
Outro problema comum é a falta de integração entre o PMP e outras áreas, como compras e comercial. Quando o plano é elaborado sem considerar restrições ou prioridades de setores cruciais, surgem inconsistências que comprometem o fluxo produtivo.
Impacto 1: Atrasos nas entregas e insatisfação do cliente
Um dos impactos mais evidentes de um PMP mal elaborado é o atraso na entrega de pedidos. Quando as datas de ordens de produção não refletem a capacidade real da fábrica, torna-se inevitável que os prazos prometidos aos clientes sejam descumpridos. Esse tipo de falha afeta a reputação da empresa e resulta em insatisfação generalizada entre os clientes, que muitas vezes buscam fornecedores mais confiáveis.
Além disso, atrasos recorrentes minam a confiança do mercado, impactando negativamente o volume de novos negócios. Clientes que enfrentam problemas de entrega podem recorrer a concorrentes mais ágeis, gerando perda de market share e colocando a empresa em uma posição desvantajosa.
Impacto 2: Aumento de WIP e estoques de produto acabado
Quando o PMP não reflete adequadamente as prioridades de produção, é comum que a fábrica opere de forma desorganizada, resultando em excesso de work-in-progress (WIP) e estoques de produtos acabados. Isso acontece porque as ordens de produção não são ajustadas às demandas reais do mercado, levando à fabricação de itens que não são imediatamente necessários.
O excesso de WIP gera custos adicionais, como espaço de armazenamento e manuseio, além de aumentar a complexidade do controle de inventário. Já o estoque de produtos acabados não vendidos compromete o capital de giro, deixando a empresa menos preparada para investir em melhorias ou responder a novas oportunidades de mercado.
Impacto 3: Compra de materiais fora do cronograma
Impacto 4: Subutilização ou sobrecarga de recursos
Outro efeito comum de um PMP de baixa qualidade é a distribuição desequilibrada da carga de trabalho. A subutilização de recursos ocorre quando ordens de produção são programadas em períodos de baixa demanda, deixando máquinas e equipes ociosas. Já a sobrecarga acontece quando há concentração de atividades em janelas de tempo apertadas, resultando em horas extras, desgaste de equipamentos e aumento do risco de falhas.
Em ambos os casos, a produtividade da fábrica é impactada negativamente, e a empresa sofre prejuízos financeiros. A falta de previsibilidade e planejamento coerente impede que os gestores utilizem os recursos de forma estratégica, afetando a competitividade do negócio.
Impacto 5: Desalinhamento entre setores
Quando o PMP não é bem estruturado, a comunicação entre os setores da empresa se torna confusa e ineficiente. Áreas como comercial, compras e produção passam a operar de forma descoordenada, com cada setor seguindo suas próprias prioridades sem considerar o impacto no fluxo produtivo.
Esse desalinhamento gera conflitos internos, duplicidade de esforços e retrabalho. Por exemplo, o setor comercial pode prometer prazos de entrega que não são factíveis, enquanto a produção se esforça para atender demandas que não foram planejadas adequadamente. Essa falta de integração prejudica a harmonia organizacional e afeta o desempenho global da empresa.
Como minimizar os impactos de um PMP de baixa qualidade?
A solução para os problemas gerados por um PMP inadequado passa por adotar práticas de planejamento mais robustas e utilizar ferramentas que integrem dados de diferentes áreas da empresa. Sistemas como o Opcenter APS, da Siemens, permitem alinhar a programação da produção às capacidades reais da fábrica, oferecendo uma visão clara e atualizada das operações.
Com o Opcenter APS, é possível elaborar um PMP que considera os recursos disponíveis, prazos de entrega e políticas de estoque. Além disso, a ferramenta promove a integração entre os setores, garantindo que todos os envolvidos no processo produtivo tenham acesso a informações precisas e consistentes.
O papel da APS3 na transformação da gestão industrial
A APS3 é especializada em soluções de planejamento e programação que ajudam empresas a superar os desafios do setor produtivo. Com expertise em ferramentas como o Opcenter APS, oferecemos suporte completo para identificar problemas no planejamento e implementar soluções que otimizem os processos e aumentem a eficiência.
Se sua empresa busca melhorar o desempenho operacional e garantir entregas dentro dos prazos, conheça nossas soluções e descubra como podemos ajudar a transformar seu negócio. Clique aqui e acesse nosso site.