MUELLER FOGÕES REDUZ EM 52% AS PARADAS DA LINHA DE MONTAGEM
Não existe uma fórmula única para o sucesso de um grupo empresarial. O Grupo Mueller, em Timbó – SC – Brasil é um exemplo espetacular de independência de gestão e cultura, com sucesso garantido em cada uma de suas unidades de negócio, não obstante a pluralidade dos métodos de administração da produção adotados.
A Mueller Fogões, uma das mais novas unidades de negócio, foi criada em 18/07/2001 para produzir fogões e fornos domésticos, dentro do conceito de mini fábricas puxadas por Kanban desde a linha de montagem. Hoje a unidade conta com cerca de 518 colaboradores, em 94 mil m2 de área construída, fabricando cerca de 118 itens diferentes, com capacidade de aproximadamente 60 mil unidades por mês entre fogões, fornos e cook-tops. O faturamento de 2014 foi de R$ 244 milhões e estão projetados R$ 266 milhões para 2015. Crescimento estimado de 10 % no aumento da capacidade produtiva sem aumentar os ativos. Isto se chama produtividade, e quem está nos bastidores deste resultado é a dupla Preactor + Lean.
DESAFIO
O arrojado sistema de administração da produção da Mueller Fogões criou, deste o início, o conceito de mini fábricas, sendo cada uma delas programada empiricamente pelo respectivo supervisor, que obedecia um quadro de Kanban com sinalizadores puxando a produção pela mini fábrica subsequente.
Apesar de todo esforço competente da equipe de Lean Manufacturing, o Kanban não estava mais trazendo os resultados esperados, essencialmente porque as linhas de montagem da Mueller Fogões são extremamente dinâmicas em seu planejamento de montagem, caracterizando:
- Alta variabilidade dos itens sendo montados de um dia para outro em cada linha;
- Alta volatilidade das quantidades e da programação em função de imprevistos.
Enquanto as mini fábricas faziam a sua própria programação, várias informações não eram consideradas, como por exemplo a disponibilidade de material interno e os fornecidos por terceiros. Consequentemente as linhas de montagem não produziam o planejado porque as mini fábricas não conseguiam responder em tempo às alterações decorrentes.
Observe-se também que a fábrica procurava suprir os componentes necessários para os itens programados nas linhas de montagem através de inventários diários e de produção urgente do item faltante e, que, invariavelmente ocorria o esquecimento de um ou outro componente, impossibilitando a montagem. Logo pode-se ver que não se tratava de uma prática de Kanban puramente.
Como consequência deste quadro, a Mueller Fogões tinha as seguintes dificuldades a superar:
- Kanban não funcionando adequadamente
- Muitas paradas da linha de montagem por falta de peças das mini fábricas
Além das paradas de linha por falta de peças, a fábrica convivia com:
- Dificuldade de balanceamento de carga máquina de vários recursos
- Dificuldade de avaliação dos gargalos
- Sem visibilidade das consequências dos imprevistos
- Sem possibilidade de compatibilizar um plano de manutenção preventiva sem prejudicar a produtividade
- Falta de análise de capacidade para dar respostas adequadas à demanda.
SOLUÇÃO
No final de 2012, face às dificuldades acima, agravadas pelo fato de que os fornecedores de MP da fábrica não foram adequadamente desenvolvidos para o ambiente JIT que se tentou implantar, os departamentos de Planejamento e de Produção começaram a procurar outras soluções além da programação puxada, implantada sem o devido sucesso.
Simultaneamente estes dois departamentos encontraram o Preactor e a APS3 em dois locais diferentes, em situações diferentes, e, de imediato perceberam que a programação fina baseada em capacidade finita, levando em consideração as restrições de materiais e dos recursos produtivos, representava uma resposta convincente ao desafio de resolver as dificuldades relacionadas no tópico acima.
Depois de realizado um DWS (Design Workshop) mostrando a viabilidade da solução, a Mueller Fogões fechou um projeto de implantação de um APS500 com a APS3. O escopo proposto então era o de sequenciar apenas a ESTAMPARIA, para desenvolver o nivelamento (Heijunka) da montagem, evitando assim a falta de peças internas que provocavam as paradas das linhas.
O projeto iniciou-se em abril de 2013. Porém, à medida que a Equipe do Projeto tomava conhecimento das potencialidades do Preactor, iniciou-se o questionamento de por que não sequenciar a fábrica toda, ao invés de sequenciar apenas a estamparia, como havia sido proposto no DWS. Mudou-se então o projeto para o sequenciamento da fábrica toda.
No final de 2013, esta tentativa de sequenciar a fábrica toda resultou frustrada, especialmente por razões culturais envolvendo a dificuldade de passar para um Planejamento central o know-how de programação de cada uma das mini fábricas.
Ocorreu então a volta ao objetivo inicial. Nova configuração do Preactor foi criada, agora dentro do escopo inicial, nivelando a montagem através do sequenciamento da Estamparia com o Preactor, conforme figura a seguir e o sistema teve seu Go Live em abril de 2014.
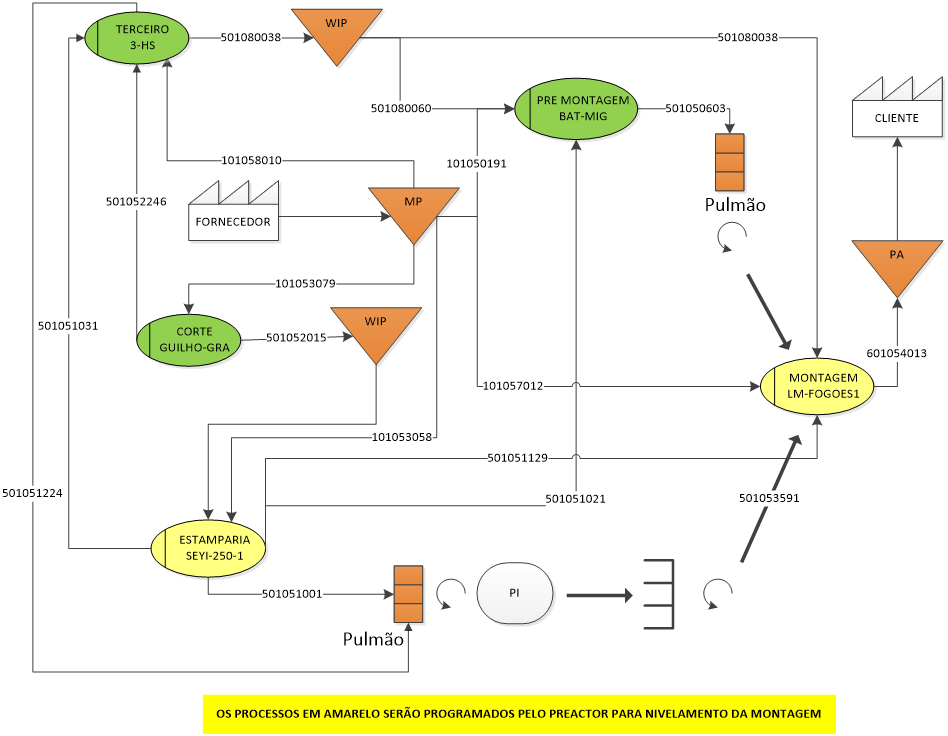
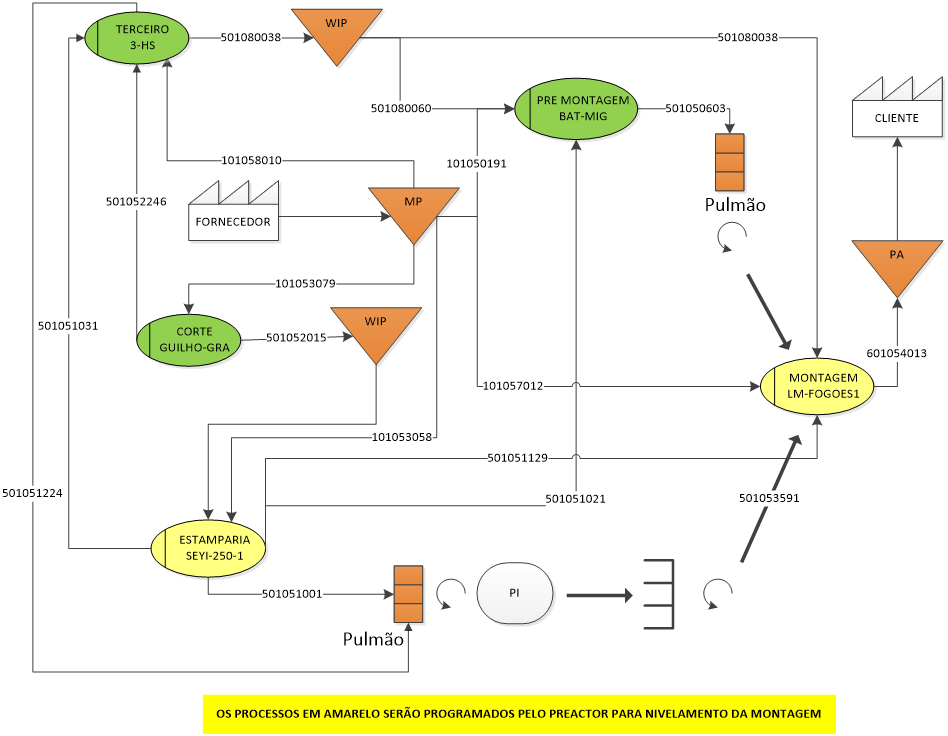
RESULTADOS
Os resultados obtidos foram marcantes, embora sequenciando apenas a Estamparia. Tais resultados já sinalizam que existe o interesse de também sequenciar a Pintura, com o mesmo princípio de nivelamento da montagem adotado para a Estamparia. No momento em que este estudo de caso está sendo escrito o projeto de sequenciamento da Pintura já se encontra em desenvolvimento.
Os resultados mais imediatos podem ser assim relacionados:
- Melhoria na visibilidade reduzindo as incertezas de produção:
– Programação de 5 dias + 1
– Sequenciamento firme de 1 dia + 2
- Maior confiabilidade do fornecedor no processo de JIT pelo fato de haver a percepção na melhoria da programação da fábrica.
- Redução dos estoques de estamparia de 3 dias para 1,5 dias de peças necessárias para a montagem futura.
- Redução significativa dos estoques intermediários (PI’s)
E o quadro abaixo sumariza o atingimento das metas do projeto e dos resultados obtidos, mostrando de forma inequívoca que valeu a pena o esforço dispendido por toda a equipe do projeto:
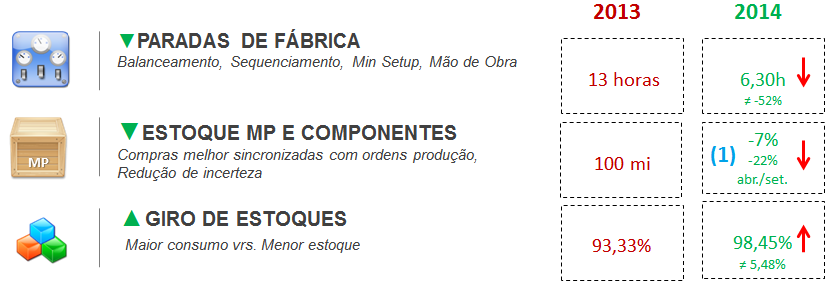
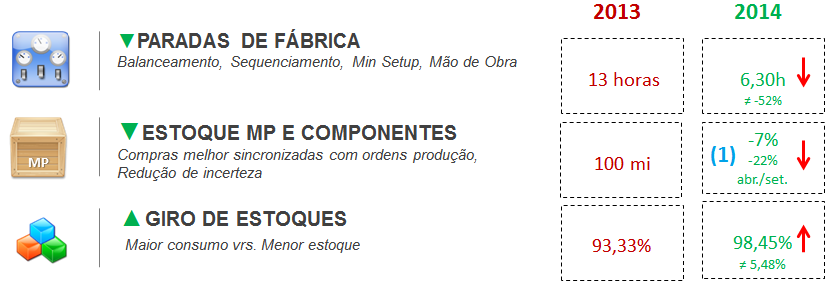
Saiba mais sobre o Opcenter APS em www.aps3.com.br/opcenter-aps/